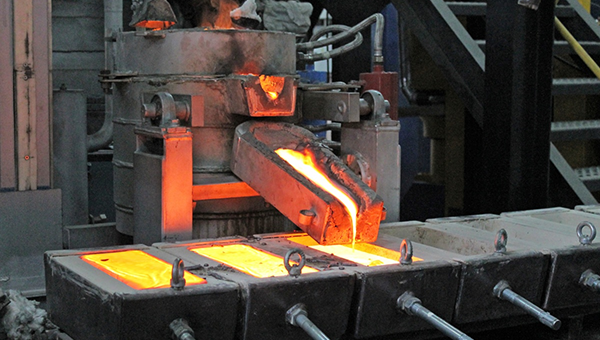
В настоящее время развиваются гидрометаллургические технологии получения цинка. Сырье, поступающее на переработку, существенно изменилось, поэтому в гидрометаллургическом производстве произошли перемены.
Так как на переработку поступают все более труднообогатимые руды, поэтому на металлургические предприятия приходят концентраты с большим количеством меди, железа и других металлов.
Одним из широко применяемых гидрометаллургических способов производства цинка является традиционный способ, включающий в себя: окислительный обжиг, выщелачивание, гидролитическую и цементационную очистку растворов, электроэкстракцию.
Вторым основным способом является автоклавное выщелачивание, которое включает: подготовку концентрата и раствора, автоклавное выщелачивание, разгрузку пульпы и рекуперацию вторичного тепла, извлечение элементной серы.
В представленной работе рассмотрены вышеперечисленные способы переработки цинковых концентратов, их преимущества и недостатки.
1. Гидрометаллургические способы переработки цинковых концентратов
1.1 Традиционный способ переработки цинковых концентратов
Гидрометаллургический метод производства цинка заключается в выщелачивании огарка серной кис¬лотой, очистке раствора от примесей, электроэкстракции цинка. Классическая схема переработки цинковых концентратов представлена на рисунке 1.

Рисунок 1 – Классическая схема переработки цинковых концентратов
Концентраты, состоящие из следующих соединений: CuFeS2, FeS2 и ZnS, а также CaCO3 и SiO2 поступают на обжиг. По данной схеме проводят окислительный обжиг с сульфатизацией для возмещения потерь кислоты в процессах выщелачивания и электролиза. Температура обжига составляет 850-970 о С. Обжиг, чаще всего, проводят в печах кипящего слоя. Допустимая влажность концентратов перед операцией составляет 8-10 %.
Выщелачивание огарка ведут в 2 стадии: нейтральная и кислая. На стадии нейтрального выщелачивания необходимо провести гидролитическую очистку раствора от Fe, Sb и As, при pH⁓5,3. После классификации пульпа направляется на сгущение. Верхний слив направляется на очистку от примесей и электролиз, а нижний – на стадию кислого выщелачивания. Далее проводится цементационная очистка от Cu и Cd, после которой раствор направляется на электроэкстракцию [1].
1.2 Высокотемпературное выщелачивание цинковых концентратов
В конце 70-х годов фирмой «Шеррит Гордон» разработан способ высокотемпературного выщелачивания. Эта технология отработана и успешно применяется на заводах в Канаде и Германии. Схема цепи аппаратов приведена на рисунке 2.

Рисунок 2 – Принципиальная схема цепи аппаратов автоклавной переработки цинковых концентратов:
1 - шаровая мельница; 2 – автоклав; 3 – самоиспаритель; 4 – теплообменник; 5 – реактор; 6 – гидроциклон; 7 – блок флотомашин; 8 – барабанный вакуум-фильтр; 9 – автоклав для выплавки серы; 10 – сборник расплава серы; 11 – фильтр-пресс; 12 – блоки серы.
Концентрат, поступающий на переработку, измельчают до крупности -44 мкм, используя шаровую мельницу. Выщелачивание проводят в горизонтальном автоклаве. Пульпу подогревают оборотным паром до 343 К и насосом закачивают в автоклав под давлением 1,85 МПа. Пульпа из автоклава поступает в первый расширительный сосуд, затем во второй, из которого она выпускается при 350 К. Используемый режим охлаждения позволяет перевести серу из аморфного состояния в моноклинную модификацию и формировать гранулы требуемой крупности.
Пульпу направляют на флотацию, используя основную и дополнительную стадии и перечистку. Пенный продукт сгущают, обезвоживают и направляют в отделение для извлечения элементной серы [2].
1.3 Сравнение гидрометаллургических методов переработки цинковых концентратов
Традиционная схема переработки имеет существенное количество недостатков, главными среди которых являются громоздкость операций окислительного обжига и выщелачивания, а также необходимость утилизации серосодержащих газов.
В связи со снижением содержания цинка и увеличением железа в концентратах ухудшились показатели традиционной технологии: уменьшилось извлечение цинка вследствие ферритообразования при обжиге [3].
Высокотемпературное выщелачивание позволило улучшить показатели процесса (Таблица 1), а именно повысить извлечение цинка на 2-5 %, сократить продолжительность операции в 2-2,5 раза, улучшить селективность извлечения цинка относительно железа, уменьшить расход серной кислоты на 10-20 %.
Таблица 1 – Показатели выщелачивания
Показатель
|
Традиционная схема
|
Автоклавная схема
|
Извлечение цинка, %
|
85-90
|
99,5
|
Расход кислоты H2SO4:Zn
|
1,3
|
1,1
|
Продолжительность, ч
|
2
|
1
|
Автоклавное высокотемпературное выщелачивание обеспечивает:
1. Полное извлечение цинка и кадмия;
2. Извлечение элементной серы;
3. Комплексное использование цинксодержащих руд, что связано с вовлечением в переработку низкосортного сырья;
4. Более высокое извлечение цинка и кадмия из-за отсутствия ферритообразования.
Заключение
В данной работе были рассмотрены основные гидрометаллургические способы переработки цинковых концентратов. Исходя из анализа данных, можно сделать вывод о том, что из-за поступления на переработку низкосортного сырья снижается качество получаемых концентратов. Это ухудшает показатели традиционной схемы переработки цинковых концентратов. Решением этой проблемы стало использование автоклавных технологий, которые позволяют повысить извлечение цинка, а также улучшить показатели процесса выщелачивания.
Список использованных источников
1. Романтеев Ю.П. Металлургия цинка и кадмия / Ю.П. Романтеев, А.Н. Федоров, С.В. Быстров. – М.: МИСиС, 2006. – 193 с.
2. Автоклавная гидрометаллургия цветных металлов / С.С. Набойченко, [и др.]. Екатеринбург, 2008. – Т.1. – 376 с.
3. Шпаер В.М. Высокотемпературное автоклавное выщелачивание низкосортных сульфидных цинковых концентратов: автореф. дис. … канд. техн. наук: 05.16.02 / Шпаер Владимир Михайлович. – СПб., 2010. – 22 с.
|